Plant Machinery Compliance Australia aims to help businesses reduce the complexity of safety evaluations and processes. Risk assessments will be done on-site to conduct our evaluations of hazards; our mission will be to identify the risks or determine them, then either remove or minimise the risks involved as necessary. We offer a methodical process to yield exceeding results, of which the information can be shared with operators and organisations.
To assist in our evaluations, PMCA utilises checklists and report documentation. Plant items are to be inspected and reviewed, adhering to the legislative requirements of Australia. We also line our strict standards with the leading industry practices and alongside international standards, as a measure to ensure the best outcome for our clients.
Throughout the inspection of the plant and machinery, hazards, risks and mitigation strategies are observed in detail. We share this document with the client, providing a clear and concise report.
Risk assessments should be conducted in several scenarios including:
- Before new procedures or operations are implemented (eg. new machinery)
- Before new plans are updated into existing ones (eg. upgrading equipment)
- When hazards are identified
Our risk assessments are carried out in Melbourne metropolitan and Victorian regional areas along with our Queensland office servicing Brisbane as well as the Gold Coast to Sunshine Coast.
Plant equipment items include (and not limited to):
- Excavator
- Truck and dogs
- Bobcats
- Concrete agitators
- Rollers
- Water trucks
- Tip trucks
Industries that require risk assessments to meet OHS requirements:
- Construction
- Meat production and processing
- Logistics
- Waste management
- Mining
- Airport
- Government
- Food and beverage
- Agricultural
- Forestry
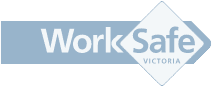
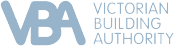
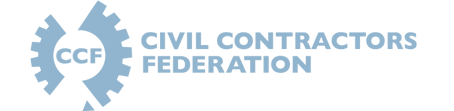
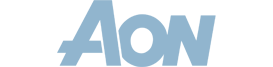